Kiln Construction Services
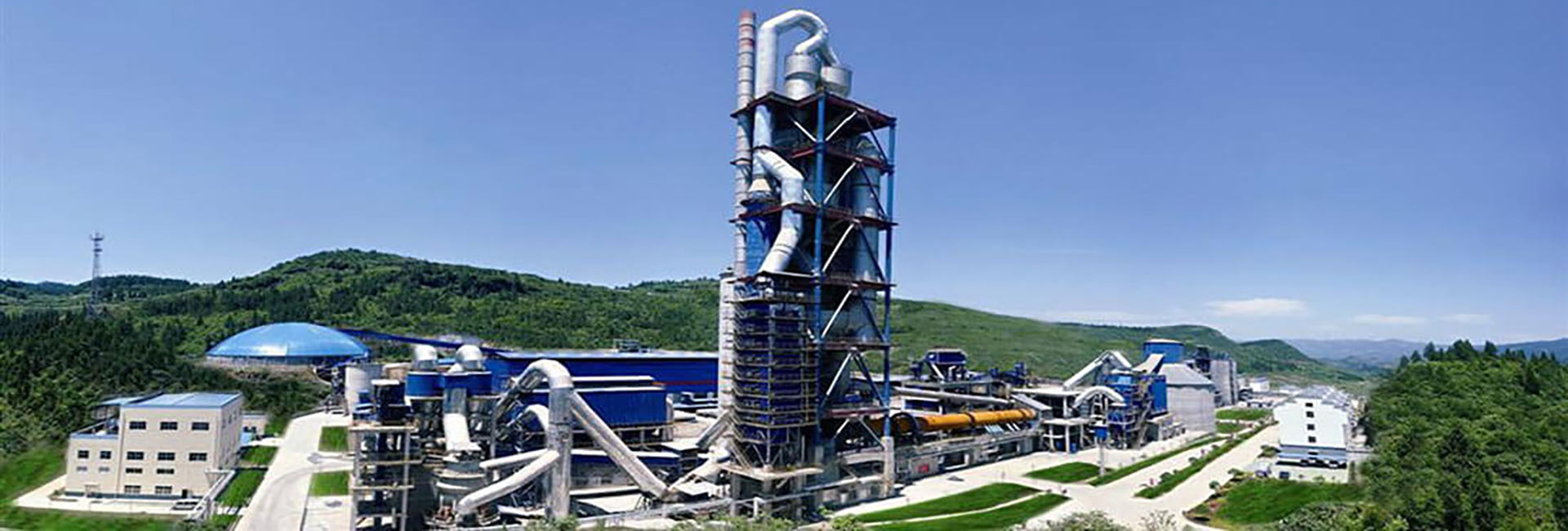
Top Kiln Construction Company
Kilns have been a cornerstone of human industry for centuries, playing a vital role in the production of ceramics, pottery, bricks, and other products. Whether you’re a craftsman looking to hone your skills or a large manufacturer looking to optimize production, the key to success often lies in the kiln you choose.
Building a furnace is a precise and complex process that requires specialized knowledge and craftsmanship, and PER Furnace Builders are the architects of these high-temperature furnaces, specializing in building structures that can withstand extreme temperatures and provide the controlled environments necessary for a variety of industrial processes.
Key Steps in Kiln Construction
Design: The first step in building a furnace is careful design planning, with PER Refractories’ engineers working closely with architects to create blueprints that take into account factors such as the desired temperature range, size, shape, and type of material to be processed.
MATERIALS: PER Furnace Construction sources high quality refractory materials, insulation and structural components. These materials are capable of withstanding extremely high temperatures, so material selection is a critical aspect of furnace construction.
Assembly: The assembly process is meticulous. Skilled craftsmen ensure that each component is precisely aligned and secured for optimal heat distribution and control.
Insulation: Proper insulation is critical to the efficiency of a kiln, and PER Furnace Builders installs multiple layers of insulation to minimize heat loss and maintain consistent temperatures inside the kiln.
Heating Systems: Depending on the intended use of the furnace, PER furnace builders utilize state-of-the-art heating systems, including electric, gas, and even renewable energy sources.
Control Systems: Modern furnaces are equipped with advanced control systems for precise temperature and atmosphere regulation. These systems typically include sensors, digital displays and programmable logic controllers (PLCs).
Testing and Calibration: Prior to delivery to the customer, furnaces undergo rigorous testing and calibration to ensure they meet specified performance standards.
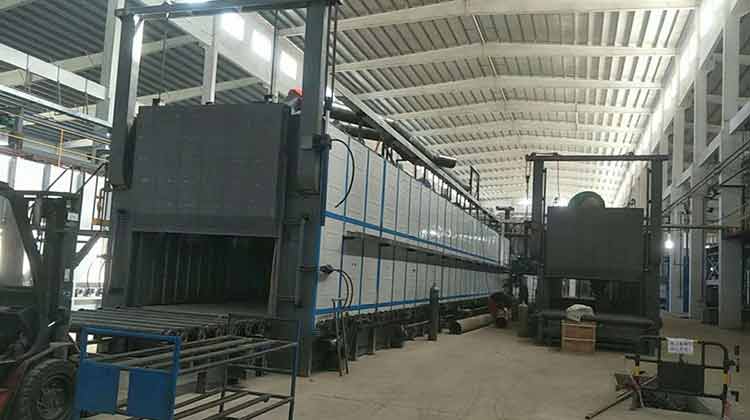
Types of Furnaces Manufactured
PER Furnace Manufacturing offers a variety of furnaces based on specific industries and applications. Here are some of the most common types:
1. Ceramic Kilns
Ceramic kilns are widely used in pottery studios, art schools, and ceramic manufacturing. They come in a variety of sizes and configurations, including electric and gas fired options. Precise temperature control is key to producing high quality ceramics, and ceramic kilns are designed with this in mind.
2. Industrial kilns
Industrial kilns are used for a wide range of applications, from sintering metal parts to baking bricks and drying wood. These kilns are often customized to meet specific manufacturing needs, making them valuable in a variety of industries, including metallurgy, construction and woodworking.
3. Glass Kilns
Glass kilns are vital in the glass blowing and glass art industries. They are designed to handle the unique heating and cooling requirements of glass products, ensuring that the final product is free of defects and distortion.
4. Heat Treatment Kilns
Heat treat kilns are used to change the properties of materials through controlled heating and cooling. This is critical in industries such as aerospace and automotive that require precise metallurgical properties.
5. Environmentally friendly kilns
With the growing concern for sustainability, PER Furnace Manufacturing is producing environmentally friendly kilns. These furnaces are designed to minimize energy consumption and emissions, in line with the global push for green manufacturing processes.
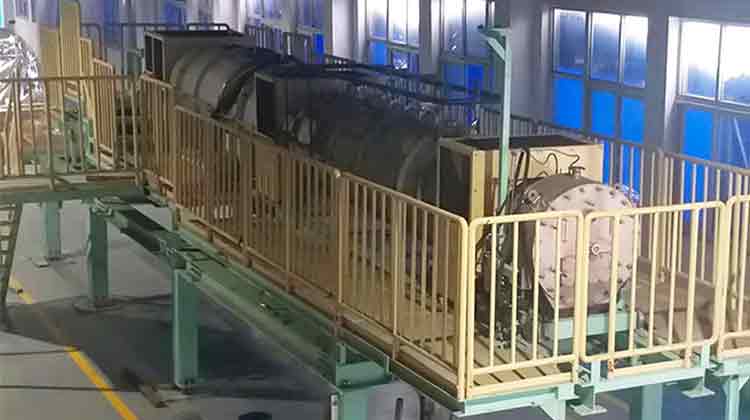
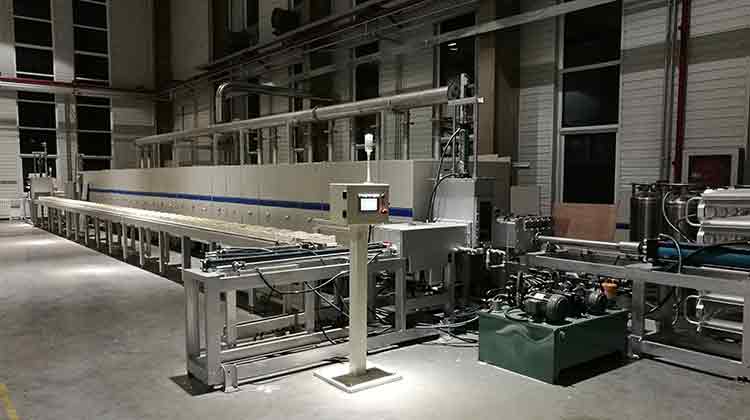
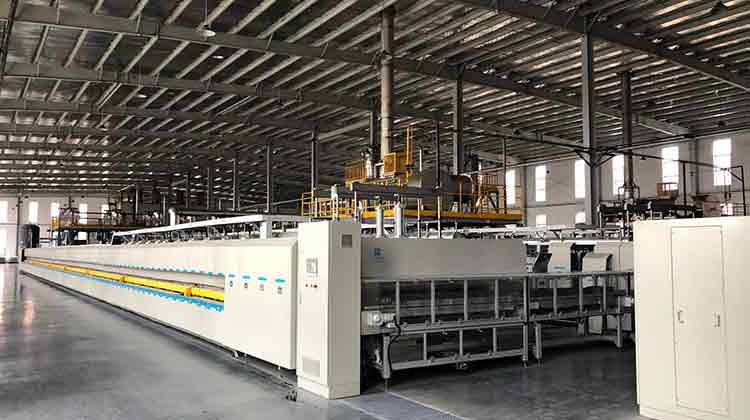
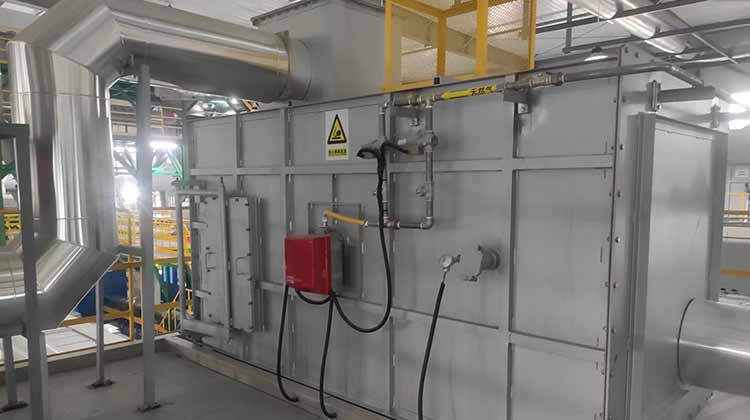
Advantages offered by PER refractory tools:
EXPERTISE: PER Refractories has a proven track record in kiln construction and a deep understanding of your industry’s needs.
Customization: Our company can customize the kiln to your specific requirements to ensure optimal performance and efficiency.
Technology: We use the latest technology and materials to build energy-efficient and reliable furnaces.
Support and service: Consider the availability of customer support, maintenance services, and spare parts to keep the kiln running optimally.
Budget: Building a furnace can be a major investment, and PER can evaluate the cost based on the quality and features offered.
The Intricate Process of Building Kilns
Building a kiln is a meticulous and highly specialized process that combines engineering expertise, craftsmanship, and a deep understanding of thermal dynamics. Kilns are essential tools in various industries, from ceramics and pottery to metallurgy and glassmaking. Let’s take a closer look at the intricate steps involved in the construction of these high-temperature ovens.
The journey of building a kiln begins with comprehensive design and planning. Kiln engineers and architects work together to develop detailed blueprints that consider various critical factors:
Purpose: The intended use of the kiln, whether for ceramics, glass, heat treatment, or other applications, dictates many design choices.
Temperature Range: The required temperature range influences the type of heating elements or burners to be used, as well as the materials for insulation.
Size and Shape: Kiln size is determined by the volume of materials to be processed. The kiln’s shape, whether rectangular, round, or custom, must facilitate even heat distribution.
Materials to be Processed: The type of materials to be processed influences the kiln’s interior lining and atmosphere control requirements.
Selecting the right materials is critical to ensure the kiln’s longevity and efficiency. Kiln construction companies carefully choose materials based on their ability to withstand extreme temperatures and harsh conditions. Key materials include:
Refractory Materials: These are heat-resistant materials used for lining the interior of the kiln. Common refractories include firebrick, refractory castables, and ceramic fiber blankets.
Insulation: Insulating materials like ceramic fiberboard, vermiculite boards, or specialized refractory insulating bricks are used to minimize heat loss and maintain a stable temperature inside the kiln.
Structural Components: The kiln’s frame and structural elements must be made of durable materials that can support the weight of the kiln and withstand thermal expansion and contraction.
Once the design and materials are finalized, the actual construction of the kiln begins. This process typically involves several key steps:
Laying the Foundation: Kilns are often placed on concrete foundations to provide stability and support.
Building the Frame: A strong frame is constructed to support the kiln’s weight. Steel is commonly used for this purpose.
Lining Installation: Refractory materials are carefully laid to line the interior of the kiln. The thickness and arrangement of these materials are crucial for insulation and heat distribution.
Insulation Layers: Multiple layers of insulating materials are added to the kiln’s exterior to reduce heat loss and improve energy efficiency.
Heating System Installation: The heating system, which can be electric, gas-fired, or use alternative heat sources, is installed according to the design specifications.
Modern furnaces are equipped with advanced control systems for precise temperature and atmosphere control. These systems include
Sensors: Temperature, pressure and atmosphere sensors are strategically placed throughout the kiln to monitor conditions.
Digital Displays: Kiln operators use digital displays to monitor and adjust temperature and other parameters.
Programmable Logic Controllers (PLCs): Programmable Logic Controllers (PLCs): Programmable Logic Controllers automate the roasting process, allowing for precise temperature ramping and soaking.
Before a new kiln is ready to be commissioned, it is subjected to rigorous testing and calibration to ensure that it meets the required performance standards. This includes
Temperature Uniformity Test: Multiple thermocouples are used to verify that the furnace maintains a uniform temperature at all times.
Atmosphere control testing: If the furnace is used for special applications such as reduction firing, the accuracy of the atmosphere control system is tested.
Safety checks: Safety features such as emergency shutdown systems are tested to ensure proper operation.
After passing all tests and inspections, the kiln is thoroughly inspected for any defects or problems. It is then disassembled, if necessary, and prepared for delivery to the customer.PER furnace construction companies often provide installation services and operator training to ensure that the furnace is successfully integrated into the customer’s operation.
In short, building a furnace is a complex process that requires a combination of engineering expertise, materials science knowledge, and skilled craftsmanship. PER Furnace Builders play a vital role in designing, assembling, and testing these high-temperature furnaces to meet the specific needs of industries ranging from ceramics to metallurgy. As such, kilns are versatile, reliable tools that allow for precise control of temperature and atmosphere, which are essential for countless manufacturing processes.
Successful Cases and Shipment
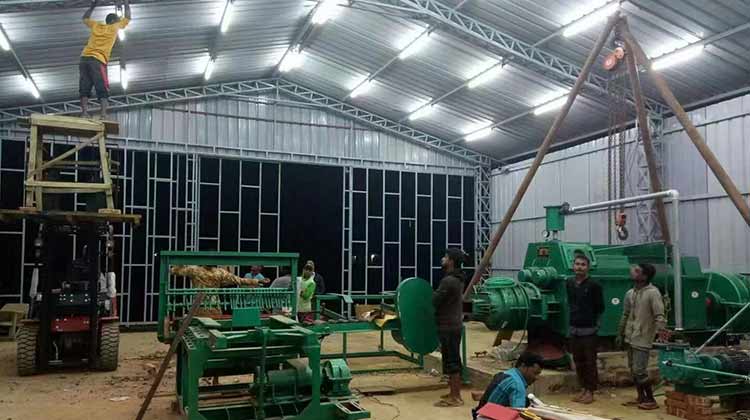
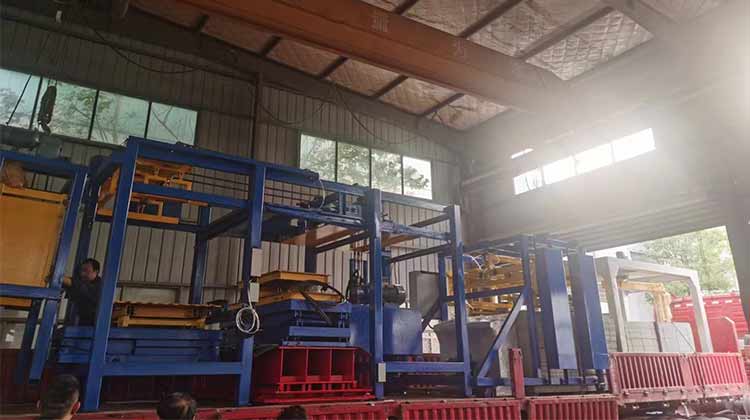
About PER Company
PER furnace manufacturing companies are the backbone of industries that rely on high-temperature processes.
These products combine expertise, craftsmanship, and technology to create reliable, efficient, and accurate furnaces for a variety of applications.
Our expertise, customization options, technology, support and budgets ensure a successful partnership and success in your chosen field.
Whether you’re producing work, manufacturing goods or advancing technology, the right kiln can be the spark that ignites your journey.
Company PER refractory is the production base of green, energy-saving, and environment-friendly new refractory materials. Our company has passed ISO9001:2008 international quality system certification and GB/T24001-2004 / ISO14001:2004 environmental management system certification, enterprise-quality inspection agency certification. Our products are sold well in more than 20 countries all over the world. They are the preferred refractory products for metallurgy, non-ferrous, petrochemical, glass, ceramics, and other refractory industries.