Chrome Bricks
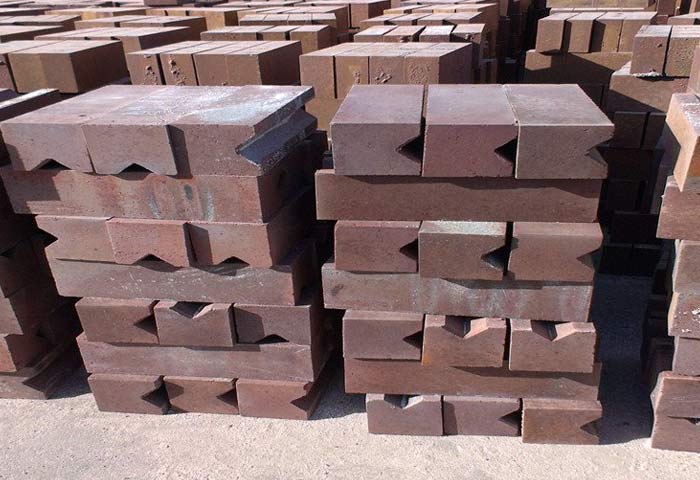
Chrome bricks are neutral bricks, mainly used as an isolation layer for acidic and alkaline refractories at high temperatures, and also used as the lining of non-ferrous smelting furnaces.
However, it should not be used in direct contact with the iron and the atmosphere changes frequently.
Chrome brick in the glass melting kiln began to be used. But only limited to dark bottles and jars glass kiln or alkali-free glass fiber kiln.
And mainly used in the high-temperature parts of the glass kiln. Such as the upper pool wall, small furnace mouth, flowing liquid hole, charging mouth, and other places, because it can significantly extend the kiln age.
PER company produces high-quality refractory bricks including refractory clay bricks, high alumina refractory bricks, refractory silica bricks, magnesia refractory bricks, mullite bricks, insulation bricks, etc.
Meanwhile, if you are interested in our refractory brick products, or if you are planning to build a furnace or kiln, you can contact us! We will reply to you promptly with professional advice and a competitive price!
More Chrome Bricks Types
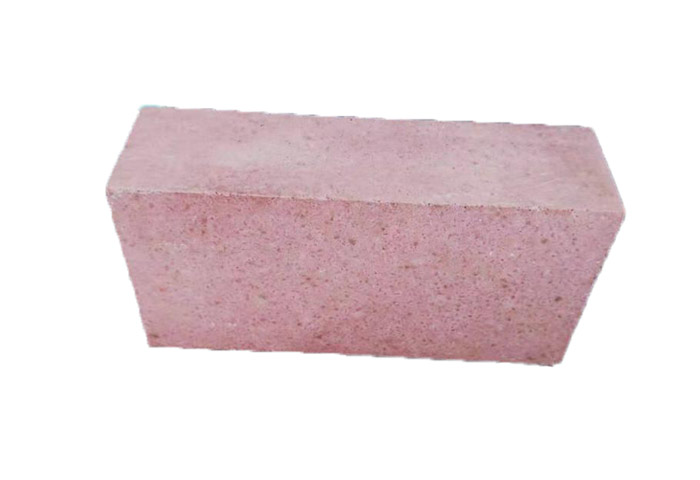
Aluminum-Chromium Bricks
AlCr brick is a high alumina brick with Al2O3 as the main component and a small amount of Cr2O3.
The sintered brick made of AlCr slag is also AlCr brick, also called AlCr slag brick. Aluminum-chromium brick than high alumina brick erosion resistance, aluminum-chromium slag brick, and high-temperature mechanical properties of good characteristics.
AlCr brick has many advantages such as high density, low porosity, high bond strength, high hardness, high load softness, good wear resistance, anti-scouring, good thermal shock resistance, strong resistance to metal melt and slag corrosion, long life, etc.
Which is widely used in various smelting equipment and other ultra-high temperature kilns.
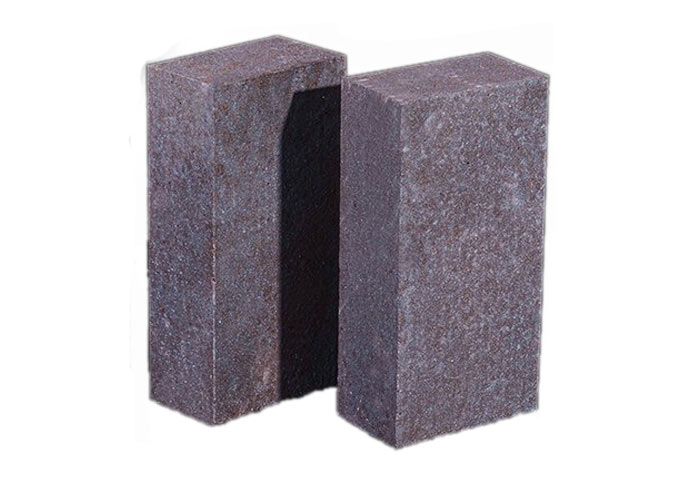
Magnesium Chrome Brick
Ordinary magnesia-chromium brick is made of sintered magnesia sand and chromite as raw materials, in appropriate proportion, by forming and high-temperature firing.
The mineral composition of the product is magnesite, spinel, and a small amount of silicate.
Ordinary magnesia-chromium brick has good resistance to alkaline slag, better resistance to acid slag than magnesia brick, better resistance to thermal shock than magnesia brick, higher load softening temperature, and good volume stability at high temperature, small shrinkage of the refired line at 1500℃.
Magnesium aluminum brick has good slag resistance, high-temperature performance, and thermal stability, the price is cheaper than magnesium spinel brick.
They are widely used in the roof of steelmaking flat furnaces and are still used in steel ladles, steelmaking furnace linings, glass kiln heat storage chambers, mixed iron furnaces, copper reflex kiln roofs, and refractory industry high-temperature kilns.
Types and Characteristics of Magnesium-Chromium Bricks
Currently, there are several types of magnesium chrome brick produced through different methods, including common brick, direct bonding brick, common sintered brick, re-bonding brick, and fusion casting brick.
1. Common Magnesia Chrome Brick
This is the traditional product, with chrome ore as coarse particles and magnesium sand as a fine powder. Or two materials using graded particle composition, the firing temperature is generally 1550 ~ 1600 ℃. The microstructure of this brick shows little direct combination between chromite particles and magnesite, mostly silicate (CMS) cementation or fissure isolation. Fang magnesite in the desolvation phase less, the matrix is rarely directly combined, the mechanical properties of this brick are poor, poor resistance to slag corrosion.
2. Directly Combined Magnesia-Chromium Brick
Directly combined with magnesium-chromium brick is developed based on ordinary magnesium-chromium brick. Its production characteristics are mainly two points, one is the use of more pure raw materials, and the second is the use of higher firing temperature. The so-called direct bonding means that there is more direct contact between chromite particles and magnesite in the brick. Because there is less Si02 in the raw material (controlled below 1% to 2%), less silicate is generated. Then the silicate is extruded into the corner of the solid phase particles using high-temperature firing, thus improving the direct bonding of the solid phase.
Direct bonding magnesium-chromium brick due to the high degree of direct bonding, so that the brick has a high-temperature strength, slag resistance, erosion resistance, scouring resistance, corrosion resistance, and excellent thermal shock stability and volume stability at 1800 ℃.
3. Common Sintered Magnesium-Chromium Brick
This product production process is characterized by a certain ratio of magnesium sand and chromite fine powder mixture of high-temperature combustion. To achieve the generation of secondary spinel and magnesia-chromite direct bonding for solid-phase reaction, the production of common sintering material. This material is used to manufacture sintered products or chemically bonded products.
Co-sintered magnesia-chromium bricks have better direct bonding and microstructural homogeneity than directly bonded bricks, with more magnesite desolvation phase and intergranular secondary spinel, co-sintered magnesia-chromium bricks have a series of better properties than directly bonded bricks, especially known for high-temperature strength, resistance to rapid temperature change and slag resistance.
4. Combined Magnesium-Chromium Brick
Electric fusion method to make magnesium-chromium mixed powder melt, through the melt precipitation crystal, the formation of a fairly uniform microstructure, magnesium-chromium spinel, and magnesite mixed crystal as the main phase composition of the raw material, the electric fusion magnesium-chromium material crushed into certain particle size, mixed molding, by firing to prepare the combined brick, or directly used to do chemically bonded brick.
About PER Refractories Company
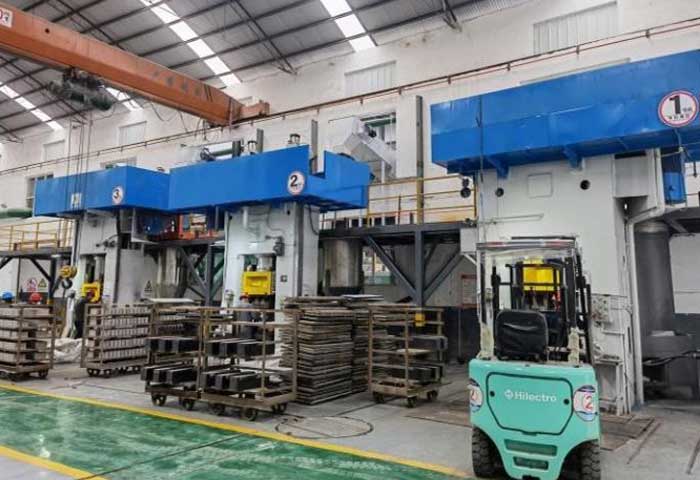
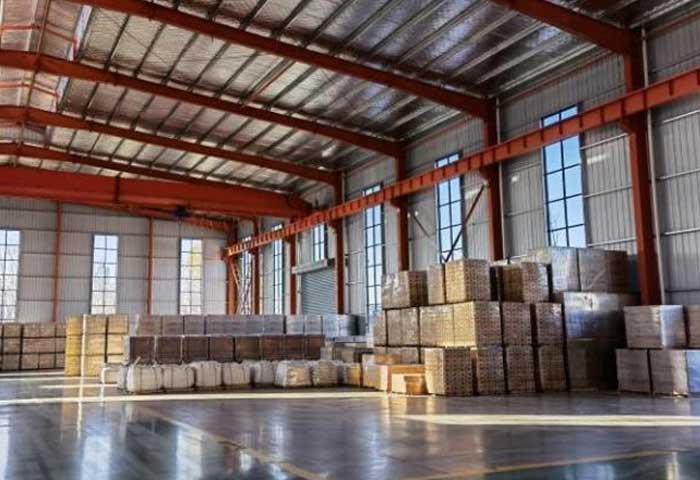
PER Refractories Company is located in Xinmi City, Henan Province, the hometown of refractory materials in China. Our company is a technology-based refractory enterprise integrating R&D, production, sales, and technical service. The rich resources and excellent quality in the territory provide unparalleled superior conditions for the production of refractory materials. Our main products are refractory clay bricks, high alumina refractory bricks, refractory silica bricks, magnesium refractory bricks, mullite bricks, insulation bricks, and other high-temperature resistant products.
Company PER refractory is the production base of green, energy-saving, and environment-friendly new refractory materials. Our company has passed ISO9001:2008 international quality system certification and GB/T24001-2004 / ISO14001:2004 environmental management system certification, enterprise-quality inspection agency certification. Our products are sold well in more than 20 countries all over the world. They are the preferred refractory products for metallurgy, non-ferrous, petrochemical, glass, ceramics, and other refractory industries.