Fire Clay Bricks For Sale
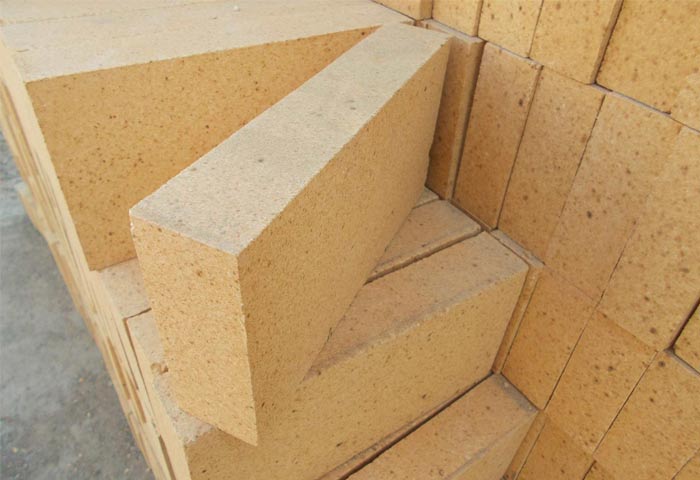
Fire Clay bricks is made of clay as the main raw material, which is mixed into plasticity and extruded by machinery. The extruded clay is called a brick billet, which is sent to the kiln after air-drying and calcined at a high temperature of 900-1000℃ to form bricks.
Clay bricks produced by PER Refractory are commonly used in blast furnaces, hot blast furnaces, glass kilns, ceramic kilns, rotary kilns, lime kilns, and other industrial kilns. Clay refractory brick products are generally divided into standard, common, and special, and can also be made according to user requirements. The common ones are common clay bricks and lightweight clay bricks. Welcome to buy cheap clay bricks from PER refractory brick manufacturers!
Characteristics Of Common Clay Bricks And Light Clay Bricks
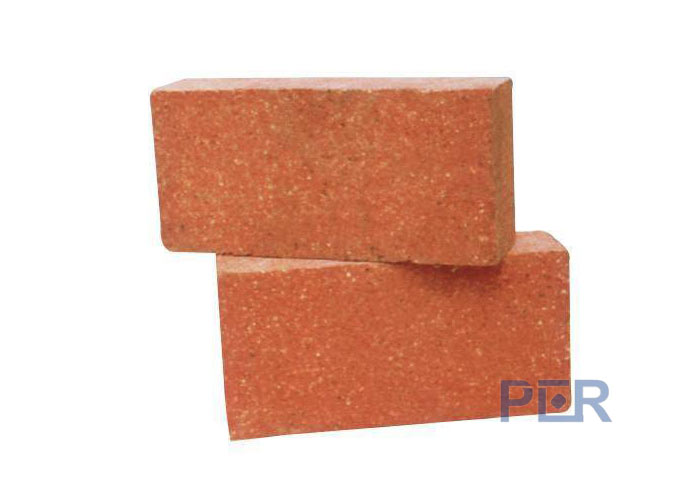
Common Fire Clay Bricks
Nature: general term for clay refractories with regular shape. The main chemical composition is alumina and silicon dioxide, but it also contains the role of melting agent iron trioxide, calcium oxide, potassium oxide, sodium oxide, titanium dioxide, etc. Ordinary solid clay bricks are locally sourced, cheap, durable, and resistant to rapid cold and heat.
Clay bricks with dimensions of 240 mm x 115 mm x 53 mm. Each brick weighs approximately 2.5 Kg when dry and 3 Kg when water is absorbed.
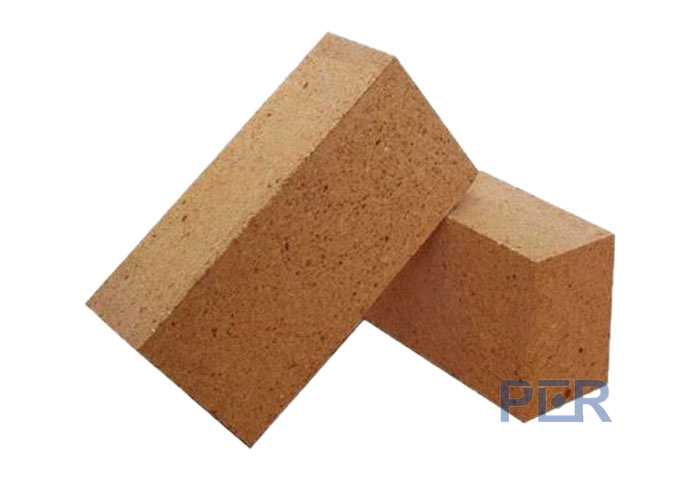
Lightweight Fire Clay Bricks
Lightweight clay bricks are lightweight refractory products containing 30%-46% Al2O3. The main principle is clay clinker or light clinker and plastic clay. Usually produced by the combustible material method, but also by chemical method or foam method to form a porous structure. It is yellowish-brown in color. The bulk density of commonly used light clay bricks is 0.75-1.20g/cm3 compressive strength is 2.0-5.9MPa, and thermal conductivity is 0.221-0.442W/(m. K) (1350℃).
The Performance Of Clay Insulation Brick Produced by PRE Refractory
PER Refractories is a leading global refractory company with factories and sales. Our manufactured or customized clay bricks for kilns have many advantages. Also, we can offer cheap fire clay brick prices. Including:
1. Low thermal conductivity, with good thermal insulation and heat preservation effect.
2. Low thermal fusion, due to low thermal conductivity.
3. Low impurity content has a very low content of oxides such as iron box alkali metal, therefore, high refractories, higher aluminum content allows it to maintain good performance under a reducing atmosphere.
4. High compressive strength in the hot state.
5. Precise appearance and size, speeding up masonry, reducing the use of refractory clay, ensuring the strength and stability of the masonry, thus extending the life of the lining
6. Can be processed into special shapes. To reduce the number of bricklaying blocks and masonry joints.
PER Refractory Have More Fire Clay Bricks Types
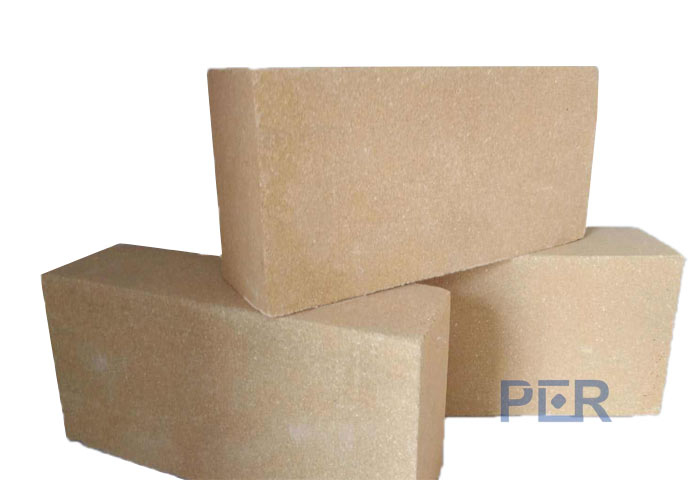
Clay Thermal Insulation Refractory Bricks
Fire clay thermal insulation refractory bricks are thermal insulation refractory products with 30%~48% Al2O3 content made of refractory clay as the main raw material.
Clay bricks are made of clinker clay, mixed, shaped, dried, sintered, and proportioned.
Clay brick thermal insulation brick is a weakly acidic refractory product, resistant to acid slag and gas erosion. It has poor resistance to alkaline compounds. However, it has good thermal shock performance.
It has the characteristics of corrosion resistance, wear resistance, good thermal shock resistance, good splicing resistance, high mechanical strength, and good volume stability at high temperatures.
Clay bricks are most widely used in industrial kiln applications.
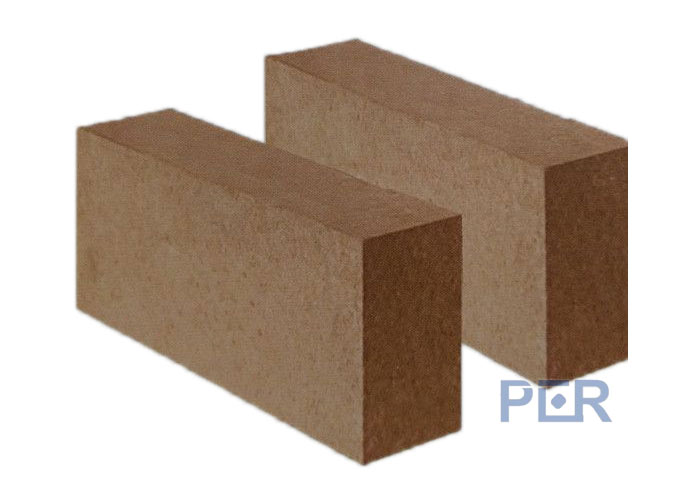
Fire Clay Bricks For Glass Kilns
The main component of clay bricks for glass melting kilns is AL2O3 content of 30~48% and SIO2 content of 50~70.
It is an acidic refractory material.
It can resist the erosion of acidic slag and acidic gas, and the resistance to alkaline material is slightly poor.
The refractoriness of this clay brick is not comparable to that of silicon brick, up to 1690~1730℃. But the load softening temperature is 200℃ lower than silicon brick.
This is because the clay brick contains nearly half of the low melting point amorphous glass phase in addition to the high refractoriness of mullite crystals.
This product is most widely used in glass melting kilns.
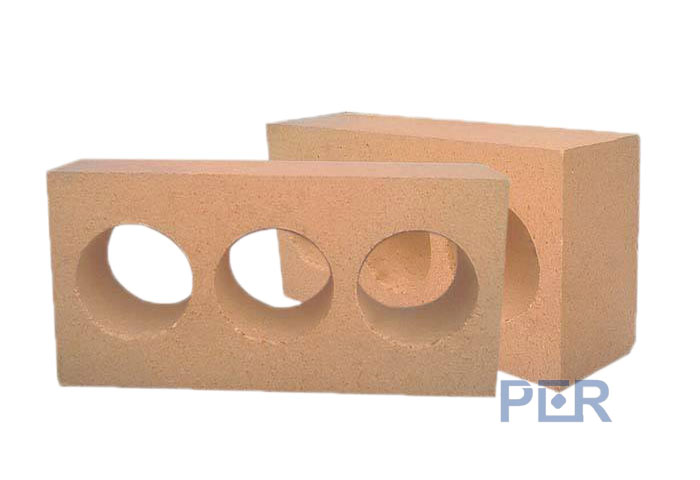
Fire Clay Three-Hole Refractory Bricks
Clay three-hole brick refers to light refractory products containing Al2o330%-46%, with clay clinker or light clinker and plasticized clay as the main principle.
Commonly used clay insulation bricks have a bulk density of 0.75-1.20g/cm3 compressive strength of 2.0-5.9MPa and thermal conductivity of 0.221-0.442W/(m. K) (1350℃).
Clay three-hole brick has a wide range of uses, mainly used in a variety of industrial kilns without contact with molten material and no erosion of the role of gas insulation layer materials, the use of temperature 1200-1400 ℃.
It is mainly used in thermal boilers, glass furnaces, cement furnaces, fertilizer gas furnaces, blast furnaces, hot air furnaces, coking furnaces, electric furnaces, and casting and steel casting bricks.
The product has excellent properties such as high refractoriness, dense bulk density, low porosity, excellent high temperature creep performance, and good volume stability.
Application Range Of Fire Clay Bricks
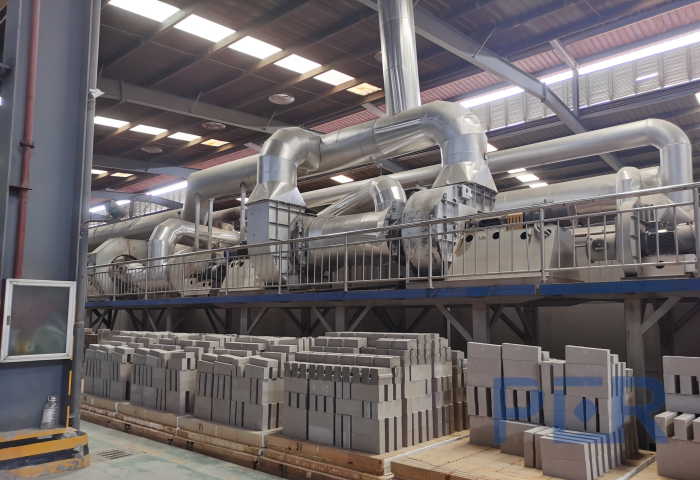
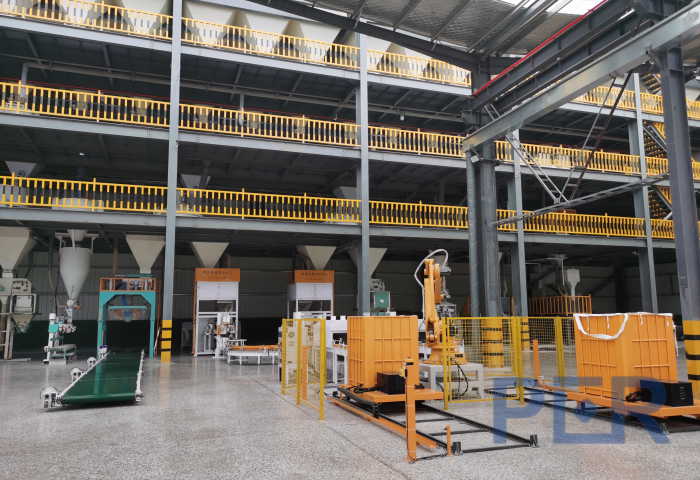
PER Refractory Produced Clay refractory bricks have a wide range of applications, mostly used in the thermal insulation layer of thermal equipment and industrial kiln protection.
It can be used in parts without strong high-temperature molten material erosion and scouring effect, some direct contact with the flame surface coated with a refractory coating to reduce the erosion by slag protection and furnace gas soot scouring, to reduce damage.
The working temperature of the product does not exceed the test temperature of the refired line change.
Definition Of Clay In Fire Clay Bricks
In line with the principle of being responsible to our customers, PER strictly controls the quality of clay insulation brick products.
Our factory ensures that the produced refractories can have good high-temperature resistance and strong slag resistance.
It can adapt to the actual boiler operating temperature of customers.
Excellent product quality is even more by the majority of new and old users have been praised and support. Welcome you to call for consultation and purchase.
PER refractories group will provide professional boiler renovation and construction solutions with a sincere service attitude.
In the past, most people would consider the definition of clay in clay bricks to be a natural decomposition product of rock. This statement, when taken as a definition of clay, has a more ambiguous meaning.
Strictly speaking, it is extremely incorrect, because this statement can be applied to other decomposition products of rocks as well.
It is analyzed by chemical analysis, observation, and thermal effects. It is known that clays differ in their chemical composition and physical properties depending on their origin and the environment in which they are produced, even in different parts of the same area, sometimes between the top and bottom layers of clay.
But all of them are mainly composed of alumina, and interspersed with a small but variable amount of other oxides.
It can be seen that the complex composition and inconsistent physical properties of clay in clay bricks make it difficult to develop a definition that is both easy to understand and concise in meaning.
The clay insulation brick manufactured by advanced and unique technology has the characteristics of high compressive strength and low thermal conductivity. When used, they can reduce the furnace wall’s heat capacity and improve the furnace’s thermal efficiency.
The clay bricks produced by the PER refractory factory are suitable for building heat insulation layers and furnace lining of industrial kilns and other thermal engineering equipment.
About PER Refractories Company
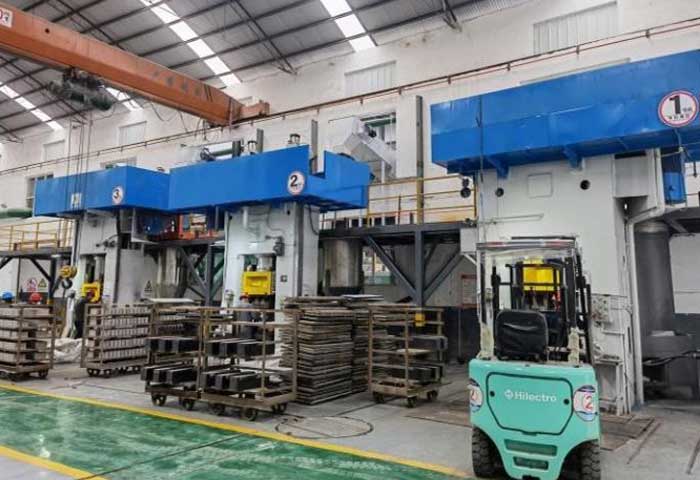
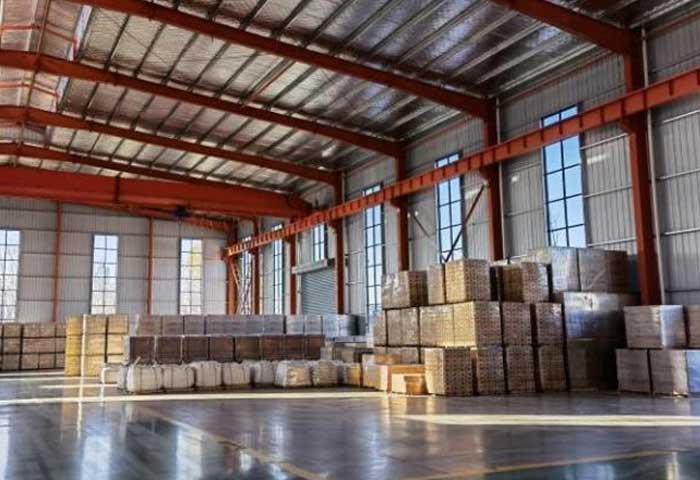
PER Refractories Company is located in Xinmi City, Henan Province, the hometown of refractory materials in China. Our company is a technology-based refractory enterprise integrating R&D, production, sales, and technical service. The territory’s rich resources and excellent quality provide unparalleled superior conditions for the production of refractory materials. Our main products are refractory clay bricks, high alumina refractory bricks, refractory silica bricks, magnesium refractory bricks, mullite bricks, insulation bricks, and other high-temperature-resistant products.
Company PER Refractory is the production base of green, energy-saving, and environment-friendly new refractory materials. Our company has passed ISO9001:2008 international quality system certification and GB/T24001-2004 / ISO14001:2004 environmental management system certification, enterprise-quality inspection agency certification. Our products are sold well in more than 20 countries all over the world. They are the preferred refractory products for metallurgy, non-ferrous, petrochemical, glass, ceramics, and other refractory industries.