What is the structure of a coke oven body? And what kind of refractory materials are used? According to the experts of Henan PER Refractories Factory, a coke oven is thermal equipment for dry distillation of coal to obtain coke and chemical products, mainly composed of a carbonization chamber, combustion chamber, roof, ramp, heat storage chamber, and small flue, etc.
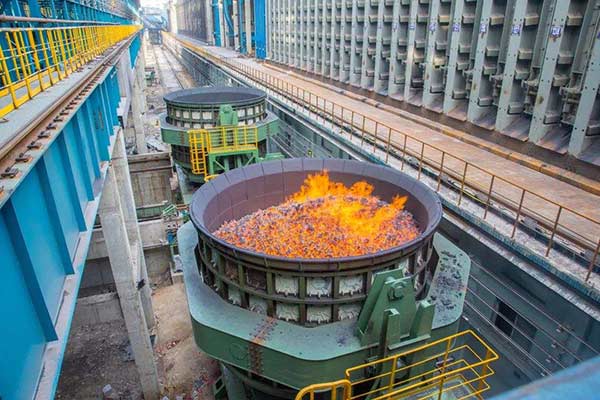
Coke Oven Body Components
1. Refractory materials for the carbonization chamber. The work of the charring chamber is cyclical, the surface temperature of the furnace wall drops to about 600’C when coal is loaded, and the surface temperature of the furnace wall rises to 1000-1100℃ at the end of coking.
Therefore, the walls and bottom of the charring chamber are built with silicon bricks. The head of the charring room at both ends, due to the sudden change of temperature when the furnace door is opened, drops from 10 00’C to below 500℃, which exceeds the temperature limit (573℃) of silicon brick volume stability.
Therefore, the stove head should be selected with good thermal shock resistance products, most of the previous choices of clay bricks, now tend to choose high-quality high alumina bricks, silica line stone bricks, and red column stone brick masonry.
2. Combustion chamber with refractory materials. The combustion room and carbonization room shared a furnace wall, the same as the carbonization room with bricks.
3. Hot air furnace roof with refractory materials. Furnace roof around the coal loading hole because of temperature fluctuations, with clay brick masonry, other parts with silicon brick masonry.
4. Refractory material for the ramp. The ramp connects the combustion chamber with the heat storage chamber, which requires a stable brick structure and can resist the effect of thermal stress. Small coke ovens with clay bricks and large and medium-sized coke ovens use silica bricks masonry.
5. Refractory materials for heat storage chamber. The single vertical wall, partition wall, bottom and lattice brick masonry of the heat storage chamber of small coke ovens are built with clay bricks, while the middle and upper masonry of the heat storage chamber of medium and large coke ovens are all built with silica bricks so that the whole coke oven can be expanded evenly.
6. small flue with refractory materials. The small flue is located at the bottom of the heat storage chamber and connected to the flue. All the small flue is lined with clay bricks.
In general, the refractory material for the coke oven is mainly silica refractory bricks. Coke oven silica bricks require precise shape and size, and have high enough bulk density, thermal conductivity, high-temperature creep, and high-temperature strength; the composition of the physical phase in the brick is dominated by scaly quartz, and the less residual quartz the better.
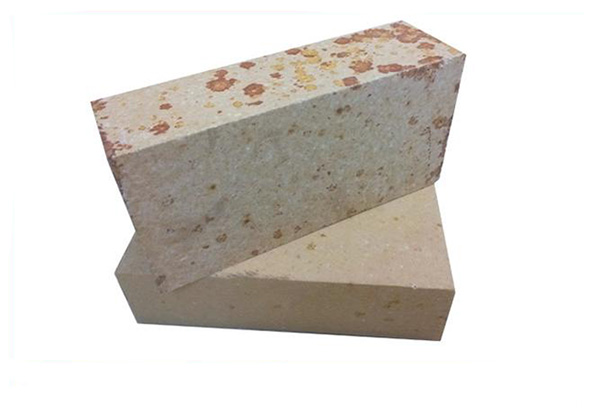
So, What Are The Basic Requirements Of Coke Ovens For Refractory Materials?
The Coke oven is the basic equipment of a coking plant, which is a kind of thermal equipment with a complex structure and continuous production. The coke oven is composed of an incinerator, charring chamber, combustion chamber, heat storage chamber, roof, ramp, small flue, and foundation.
The masonry of a 42-hole coke oven requires 6,557 tons of refractory materials, of which 4,352 tons, or 66.4%, are silica bricks. Coke ovens in 20 to 25 years of the operation cycle, most of the masonry is not easy to hot repair. Therefore, the refractory materials for coke ovens must be able to adapt to the requirements of the coking production process and be durable and reliable.
Based on the characteristics of coke production, refractory materials for coke ovens have their basic requirements. The different parts of the coke oven body have different performances due to the different tasks, temperature, structural load, mechanical damage, and media erosion.
The partition wall between the coking room and the combustion chamber can reach a temperature of more than 1550°C in the main fire escape during normal production.
This wall is the carrier of the heat required for coking, which requires that the furnace material should have good high-temperature thermal conductivity.
This partition wall also bears the structural load of the upper masonry and the gravity of the coal-loading car at the top of the furnace. At the same time, it is required that the furnace material should have the performance of a high-temperature load without deformation.
The wall surface of the carbonization room is subject to the erosion of ash, slag, moisture, and acid gas, methane also penetrates the brick voids to produce carbon deposits, and the bottom of the main fire escape is subject to the slagging erosion of coal dust and dirt. Therefore, it is required that the furnace material should have high-temperature corrosion resistance.
The temperature of the wall of the charring room drops sharply from about 1100℃ to 600-700c when coal is loaded, so the furnace material is required to have the performance of resistance to high-temperature drastic change above 600℃. Due to the influence of pushing coke, it also requires the carbonization chamber bottom brick to have high wear resistance performance.
The temperature difference between the inner and outer wall of the combustion chamber head is very different, and the temperature changes a lot when loading coal, and it is also affected by the pressure of the protection plate, which requires that the furnace building materials should have better resistance to drastic temperature changes and better pressure resistance.
The temperature difference between the upper and lower layers of the lattice brick used in the heat storage chamber reaches about 1000℃, and the temperature difference between the updraft and downdraft is between 300~, which requires the lattice brick material should have the characteristics of high bulk density and strong resistance to drastic temperature changes.
It is reported that the small flue in the updraft when the temperature is lower than 100 ℃, while in the down draft is higher than 300 ℃, refractory brick gas channel by the action of room temperature gas and water vapor, so both require furnace building materials in 300 ℃ below should have the performance of resistance to drastic changes in temperature.
In short, masonry refractory materials firebricks for coke ovens should have the following characteristics
The load softening temperature is higher than the maximum temperature of the used part.
Resistance to temperature changes within the temperature range of the part to be used.
Resistance to various media that may be encountered in the use area.
The charring chamber – combustion chamber wall has good thermal conductivity, and the lattice brick has good heat storage properties, etc.
The refractories firebricks, thermal conductivity, thermal expansion, porosity, bulk density, high-temperature load softening temperature, high-temperature volume stability, resistance to drastic temperature changes, etc. of commonly used refractory materials for coke ovens should meet the requirements.