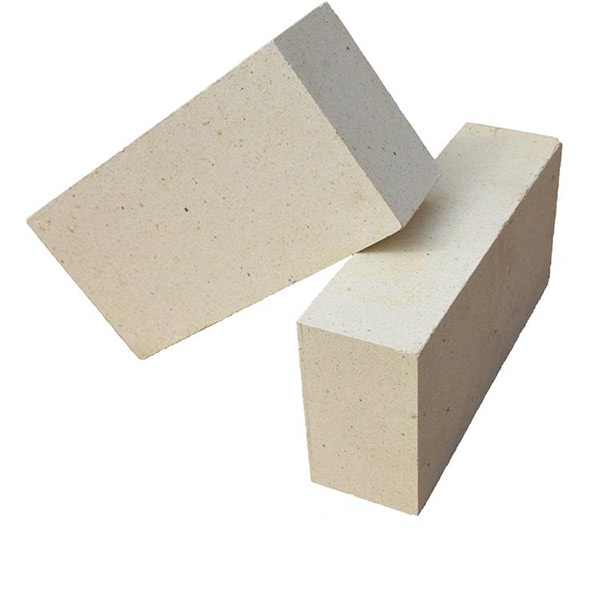
Properties of High Alumina Refractory Bricks
One of the important working properties of high alumina refractory bricks is their structural strength at high temperatures, which is usually assessed by the load softening deformation temperature.
In recent years, high-temperature creep has also been measured to reflect its high-temperature structural strength. The test results show that the load softening temperature increases with the increase of Al2O3 content.
For refractory bricks with Al203 content below 70%, the load softening temperature depends on the ratio between the number of mullite crystalline and liquid phases and increases with the number of mullite.
The number and nature of the liquid phase have a significant effect on the load softening temperature.
Therefore, reducing the impurity content in raw materials is beneficial to improve the load softening temperature and high temperature creep.
For mullite-corundum refractory bricks with Al203 content of 70%-90%, the increase of load softening temperature was not significant with the increase of Al203 content.
This is due to the partial softening of mullite crystals at high temperatures and a slight increase in the number of melt impurities that interact with dignity crystals.
In particular, the Ti02. Fe203 composition increases slightly with the increase of Al203 content in the raw material, which changes the quantity and nature of the liquid phase at high temperatures.
Due to the large increase of Ti02. Fe203 composition in the glass phase, the number of glass phases increases, and the viscosity decreases. This is the obvious impact on the load softening temperature and high-temperature creep to improve the crux of the problem is not much.
Only when the refractory brick transition to almost completely corundum composition, that is, refractory brick Al203 content of 95% or more, the high-temperature structural strength is significantly improved.
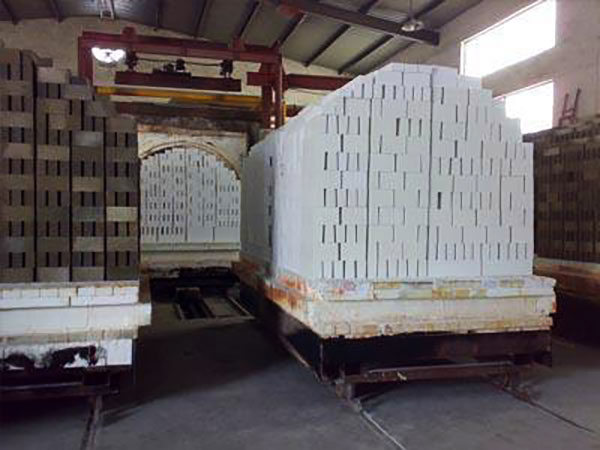
Seismic Resistance Of High Alumina Refractory Bricks
High alumina refractory brick thermal shock resistance than clay bricks, which is closely related to the mineral composition of the refractory bricks.
I, II high alumina brick is worse than III high alumina brick. In the production of often by improving the refractory brick particle structure characteristics or in the ingredients to add a certain amount of synthetic cordierite and other minerals to improve the thermal shock resistance of refractory bricks:
According to PER refractory plant experts, the slag resistance of high alumina refractory bricks increases with the increase of Al203 content.
However, its resistance to alkaline slag is lower than that of alkaline refractories. The reduction of impurity content is beneficial to improve slag resistance.
At the same time, increasing the density of refractory bricks: and reducing the porosity is also effective measure to improve their slag resistance.
High alumina bricks have higher thermal conductivity than clay bricks, which is related to the reduction of the glass phase and the increase of mullite or corundum crystals in high alumina refractory bricks.
Refractory Material Must Have The Requirements
1. To adapt to the high-temperature operation requirements, should have a sufficiently high temperature without softening and melting.
2. Able to withstand the load of the furnace and the stress applied during operation, and at high temperatures without loss of structural strength, softening deformation, and collapse, usually expressed in terms of load softening temperature.
3. Stable in volume at high temperature, the kiln masonry or cast body does not crumble due to excessive expansion of the product, or cracks due to excessive shrinkage, reducing the service life. Usually measured by the coefficient of linear expansion and refired shrinkage.
4. Refractory material is greatly affected by the operating conditions of the furnace, the temperature changes sharply and unevenly heated so that the furnace body is easy to damage. Therefore, it is required to have a certain degree of thermal shock resistance.
The quality of the refractory material depends on its nature, which is the standard criterion for evaluating the quality of the products. The correct and reasonable selection of refractory materials is also based on their properties as an important basis.
PER Refractories Factory refractory castables products are recommended: high alumina refractories, and kinds of clay refractories.