
Generally speaking, the temperature rise curve is determined by the refractory bricks used in the rotary kiln. If you are constructing the kiln yourself, you should ask the refractory brick manufacturer to provide the corresponding temperature rise curve. If you are a contractor, the construction team will warm up according to the product characteristics and construction characteristics. It is recommended that the package work and materials, ensure product quality and construction quality. PER Refractories can be consulted if you have any relevant needs.
So, here comes the question. On what basis is the temperature rise curve of a rotary kiln determined? What is the difference between the heating curve of a 5000t kiln and a 2500t kiln?
The temperature rise curve is mainly based on the refractory material built in the rotary kiln, for example, 150°C is the process of removing gravity water from the refractory, and 300°C is the removal of crystallization water, etc.
The temperature rise curve depends on the type of refractory you use, and the curve is different for different types of refractories, and generally refractory manufacturers will provide the temperature rise curve.
The main difference between 5000t and 2500t is the time of heating up, but the heating up node is roughly the same.
Silica Mullite bricks Brick Temperature Rise Curve
Silica Mullite bricks are refractory bricks made of mullite and rhodochrosite and silicon carbide and special homogenized bauxite as the main raw materials, which are formed by high pressure and fired at high temperature.
Production Process
Silica Mullite bricks are characterized by good high-temperature resistance and wear resistance, corrosion resistance, low thermal conductivity, low energy consumption, etc. Currently, they cover the cooling and transition zones of the vast majority of cement kilns.
Silica Mullite bricks not only have very good thermal shock resistance but also thermal conductivity, which completely meets the use of cement kilns.
According to the use of proof, the outside of the cement kiln requires a temperature of no more than 320 degrees, while the temperature detected after the use of Silica Mullite bricks is basically only 250-280 degrees, which greatly reduces the surface temperature of the kiln cylinder and reduces energy consumption.
The resistance to heat of the Silica Mullite brick is also very good, and its load softening temperature can reach 1600 degrees. The load softening temperature can reach 1600 degrees Celsius, while the carrier in cement kilns is generally about 1400 degrees Celsius, so it can be used repeatedly for 1 year without any problem. And its wear resistance is also excellent, and fully meets the standard requirements of refractory materials.
Scope Of Application
Silica Mullite brick configuration is highly adaptable. The traditional configuration of refractories is usually configured with different properties of refractories such as spinel bricks, magnesium-chromium bricks, and anti-spalling bricks in the kiln mouth, front transition zone, rear transition zone, and decomposition zone respectively. The Silica Mullite red brick can cover all the process belts other than the firing belt.
Silica Mullite bricks have good wear resistance and shock stability and have achieved good results in the use of a rotary kiln. The service life in the secondary firing zone and transition zone of cement rotary kiln is better than that of spinel bricks.
The main reason is that spinel bricks form an erosion zone due to alkali erosion in use, which causes cracks and spalling on the hot surface and accelerates the damage.
While the Silica Mullite brick structure is dense, mullite and SiC crystals are stable, plus the formation of a continuous SiO2 dense layer on the brick surface prevents the erosion of gas and melt. Together with the high thermal conductivity and low coefficient of thermal expansion of SiC, the products have good thermal and seismic stability.
These performance characteristics make the SiMo brick less likely to break and produce spalling, and because the thermal conductivity is lower than that of magnesium materials, the barrel is not overheated. This not only ensures the normal operation of the rotary kiln barrel but also saves fuel.
In addition, the performance of Silica Mullite bricks is also significantly better than that of spalling-resistant high alumina bricks and phosphate high alumina bricks with better wear resistance. Therefore, various grades can be produced and selected by cost performance for different section belts, and the range of use in rotary kilns is expanding.
AZM1680 Silica Mullite brick has a balance of high-temperature resistance and wears resistance. AZM1680 silicone brick has a high load softness and excellent resistance to high temperatures.
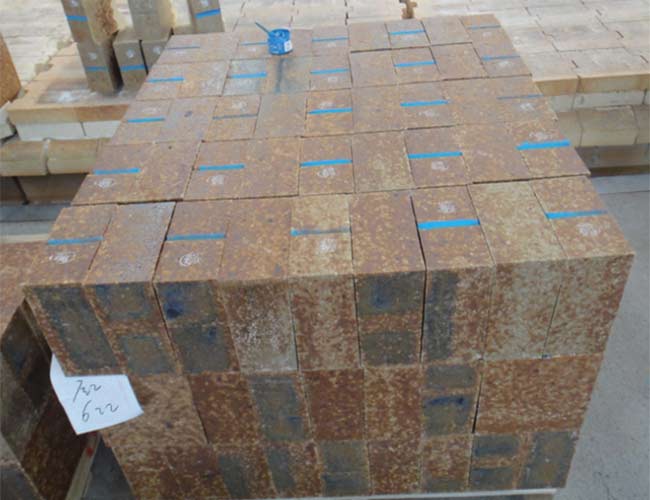
Summary
PER is a professional refractory material manufacturer with high quality and low price. PER adopts an automatic production process and equipment and introduces advanced management and quality inspection system to ensure that each batch of refractory bricks and refractory castable can meet the requirements of users.