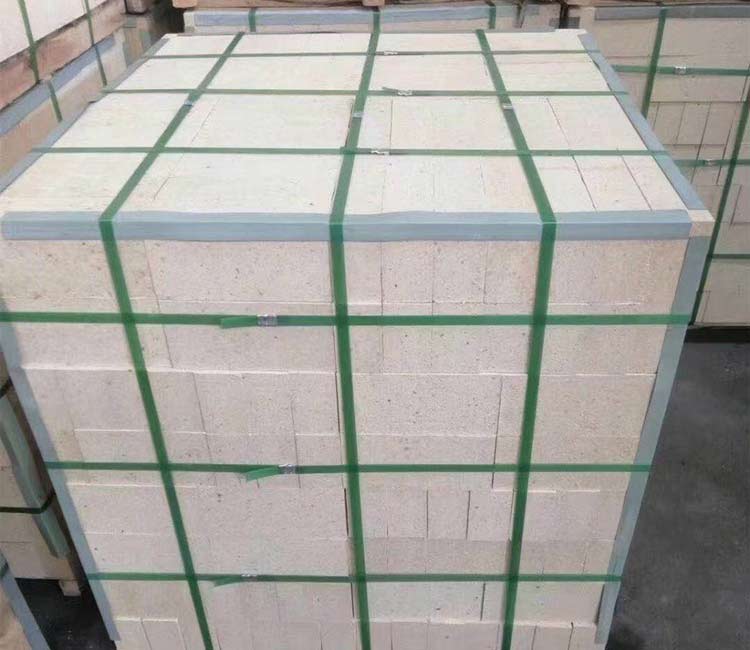
What Are Refractory Bricks?
Refractory bricks are called fire brick for short, refractory materials made of refractory clay or other refractory raw materials. Light yellow or brownish, mainly used for smelting furnaces, can withstand 1,580 ℃—1,770 ℃ high temperature.
Refractory bricks are generally divided into two types, namely, amorphous refractories and fixed refractories.
Indefinite refractory material: also called castable, is a variety of aggregates or aggregates and one or more kinds of adhesives and mixed powder particles, when used with one or more kinds of liquid must be mixed well, with strong fluidity.
Shaped refractory materials: general refractory bricks, the shape of the standard rules, but also according to the need to build cut when the temporary processing.
So, let us PER refractory company explain it to you.
Indicators Of Refractory Bricks
1. Refractories
Refractories are the temperature at which the material reaches a specific degree of softening under the action of high temperature, characterizing the performance of the material to resist the action of high temperature.
Fire brick products’ refractories mainly depend on their mineral composition, the number of fusible impurities, the combination of minerals, and the degree of diffusion of each component.
Some commonly used refractory products refractories reference: clay bricks 1300 ~ 1650 ℃, high alumina bricks 1500 ~ 2000 ℃, silicon bricks 1600 ~ 1730 ℃, magnesium bricks greater than 2000 ℃.
2. Load Softening Temperature
Load softening temperature is also known as load deformation temperature, referred to as the load softening point. Refers to the refractory products in the specified heating conditions, the temperature of deformation under constant pressure load.
It indicates the product’s resistance to the simultaneous action of high temperature and load. To a certain extent, it indicates the structural strength of the product under similar conditions of use.
It also indicates that at this temperature, the product has obvious plastic deformation, which is an important quality indicator of the use performance.
Carbon bricks are not easily deformed when working at high temperatures.
The load softening point of clay bricks is lower.
The load softening temperature of high alumina brick is higher than that of clay brick.
3. Apparent porosity
Apparent porosity is also known as open porosity. Refers to the volume of open pores in refractory products and the percentage of the total volume of the product.
Apparent porosity not only reflects the dense degree of refractory materials but also characterizes the manufacturing process of particle size composition, molding, and firing as reasonable.
Except for lightweight refractory products, low porosity raw materials or products are beneficial for improving product quality, increasing the mechanical strength of products, reducing the surface area in contact with slag, and extending service life.
The porosity of refractory bricks is distributed among coarse particles, bonding agents, and between coarse particles and bonding agents, and its presence improves the thermal insulation of refractory bricks and reduces the erosion resistance of refractory bricks.
The apparent porosity of magnesium bricks is in the range of 14% to 20%, high alumina bricks can reach 18% to 23%, and the apparent porosity of clay bricks is higher, in the range of 18% to 26%. Increasing the molding pressure and increasing the sintering temperature can reduce the porosity of the products.
4. Room Temperature Compression Strength
At room temperature, a pressure testing machine is used to load a specimen of refractory brick of a specified size at a specified rate until the specimen is broken. And according to the recorded maximum load and the area of the specimen under load to calculate the room temperature compressive strength.
The normal temperature compressive strength of refractory bricks is generally greater than 30 MP.
Refractory brick compressive strength mainly depends on the strength of the raw material particles themselves, the solidity of the particles bonded to each other, the number of pores and the form of existence, and the size of the bonding ability of the added bonding agent.
5. Reburning Line Change
Reburn line change is a refractory brick to express the high-temperature volume stability of the index. It refers to the residual expansion or contraction of the refractory brick specimen after it has been heated to a specified temperature and held for a certain time, and then cooled to room temperature.
This process results in an irreversible change in the size (length) of the refractory brick, expressed in % as the rate of change of the refired line.
Under certain conditions, residual expansion is less harmful.
The proper residual expansion will close the masonry joints and improve the life of the masonry, but excessive expansion will destroy the shape of the masonry and cause it to collapse.
Excessive residual shrinkage will make the masonry brick joints increase, affecting the integrity of the masonry, and even making the masonry collapse.
A variety of different materials of refractory bricks allow refired line change rate generally not exceed 0.5% ~ 1.0%.
6. Thermal Shock Stability
Refractory brick resistance to rapid changes in temperature without damage to the performance becomes thermal shock stability. This performance is also known as resistance to thermal shock or rapid temperature change resistance.
Refractory brick to withstand 1100 ℃ to room temperature as a measure of the number of rapid cooling and heating.
Refractory fire brick is a non-homogeneous brittle material, compared with metal products, due to its more significant thermal expansion, smaller thermal conductivity, elasticity, low tensile strength, etc. The ability to resist thermal stress without damage is poor, resulting in its lower thermal shock resistance.
Summing up
After reading this explanation, I believe you have a very good understanding of the indicators of refractory bricks. Each index determines the use of refractory bricks and the service life of refractory bricks. PER Refractories is a company specializing in the production and sales of refractory materials. We have decades of manufacturing experience, which ensures that we can provide you with the most suitable refractory material for your different project needs. You can always contact us for more product information and discounts.